News Release
Development Trend of Domestic Automotive Hardware Stamping Industry
Source:
Release time: 2023.06.05
With the rapid development of industries such as sedans, communication electronics, and household appliances, the demand for metal stamping and other components is increasing day by day. Many multinational enterprises have established production lines in China and also moved their automobile production supporting factories to China. The procurement volume of parts from China has also grown rapidly year by year. German and American automobile factories have now included the products of our stamping parts factories in their global acquisition chains, driving the rapid development of related professions in China. Moreover, with the optimization of production technology by local automotive companies, the advantages of domestic automotive stamping parts in the world market will be further highlighted.
Low cost and high quality call for cutting-edge technology
The Chinese automotive stamping market is showing strong growth momentum. Without the low cost of domestic stamping molds, there would be no rapid development of domestic brand cars, but low cost does not mean low level. The rapid development and improvement of quality of domestic cars cannot be separated from the improvement of the level of domestic stamping parts. In order to meet the needs of consumers, automobile manufacturers are constantly introducing new models, which requires the continuous updating and upgrading of automotive stamping parts. This will inevitably put forward higher technical requirements for automotive stamping parts, which is also an inevitable trend in the automotive stamping mold market. How to improve the automation level, precision, service life, and quality of stamping parts is an important goal that domestic automotive stamping parts manufacturers need to achieve at present.
Rapid development of digital molds and automated processing
Digital mold technology is an effective way to solve many problems faced in the development of automotive molds. Consider and analyze manufacturability during design to ensure the success of the process. CAE assists in analyzing and simulating the stamping process, predicting and solving potential defects and forming problems. And mold processing automation refers to the development of CNC machine tools equipped with dual workbenches, automatic tool change devices (ATC), optoelectronic control systems for automatic processing, and online measurement systems for workpieces in automotive mold enterprises. From medium to low speed processing to high-speed processing, processing automation technology has developed rapidly.
The Development Trend of Automotive Stamping Dies
The focus of development in automotive panel molds is on high technical requirements for large and medium-sized panel molds for mid to high-end sedans, especially for external panel molds. Stamping molds for unequal thickness and high-strength plates, as well as large-scale multi-station progressive and continuous molds, will have rapid development. According to Shenzhen Chengruifeng Technology, the development focus of multifunctional and multi-station progressive molds is on high-precision, high-efficiency, and large-scale, long-life progressive molds. The focus of development in precision stamping dies is on thick plate precision stamping dies and large precision stamping dies, and continuously improving mold accuracy.
Shenzhen Chengruifeng Technology Co., Ltd. From careful material selection in the early stage to hardware mold production in the later stage, precise control of the production process details and costs, high-precision precision parts processing accuracy reaches ± 0.001MM, and stamping mold accuracy reaches ± 0.01MM. At the same time, we have introduced hundreds of precision stamping equipment from Germany and Japan, ranging from 25T to 300T, to meet the needs of automotive hardware stamping parts in multiple aspects. We have set up strict inspection and control personnel for each layer of process flow, striving for excellence.
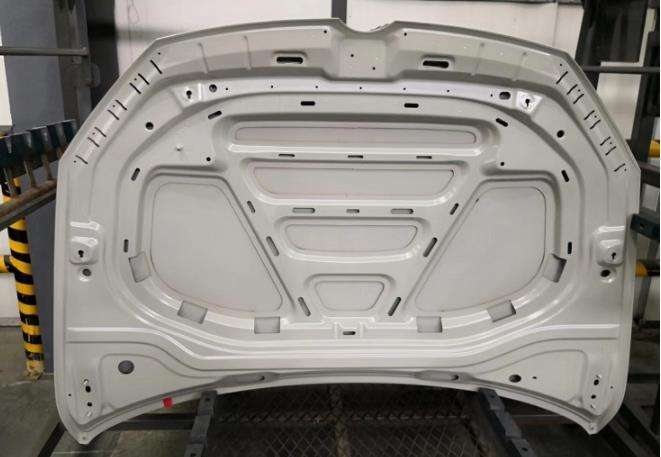
The Chinese automotive stamping market is showing strong growth momentum. Without the low cost of domestic stamping molds, there would be no rapid development of domestic brand cars, but low cost does not mean low level. The rapid development and improvement of quality of domestic cars cannot be separated from the improvement of the level of domestic stamping parts. In order to meet the needs of consumers, automobile manufacturers are constantly introducing new models, which requires the continuous updating and upgrading of automotive stamping parts. This will inevitably put forward higher technical requirements for automotive stamping parts, which is also an inevitable trend in the automotive stamping mold market. How to improve the automation level, precision, service life, and quality of stamping parts is an important goal that domestic automotive stamping parts manufacturers need to achieve at present.
Rapid development of digital molds and automated processing
Digital mold technology is an effective way to solve many problems faced in the development of automotive molds. Consider and analyze manufacturability during design to ensure the success of the process. CAE assists in analyzing and simulating the stamping process, predicting and solving potential defects and forming problems. And mold processing automation refers to the development of CNC machine tools equipped with dual workbenches, automatic tool change devices (ATC), optoelectronic control systems for automatic processing, and online measurement systems for workpieces in automotive mold enterprises. From medium to low speed processing to high-speed processing, processing automation technology has developed rapidly.
The Development Trend of Automotive Stamping Dies
The focus of development in automotive panel molds is on high technical requirements for large and medium-sized panel molds for mid to high-end sedans, especially for external panel molds. Stamping molds for unequal thickness and high-strength plates, as well as large-scale multi-station progressive and continuous molds, will have rapid development. According to Shenzhen Chengruifeng Technology, the development focus of multifunctional and multi-station progressive molds is on high-precision, high-efficiency, and large-scale, long-life progressive molds. The focus of development in precision stamping dies is on thick plate precision stamping dies and large precision stamping dies, and continuously improving mold accuracy.
Shenzhen Chengruifeng Technology Co., Ltd. From careful material selection in the early stage to hardware mold production in the later stage, precise control of the production process details and costs, high-precision precision parts processing accuracy reaches ± 0.001MM, and stamping mold accuracy reaches ± 0.01MM. At the same time, we have introduced hundreds of precision stamping equipment from Germany and Japan, ranging from 25T to 300T, to meet the needs of automotive hardware stamping parts in multiple aspects. We have set up strict inspection and control personnel for each layer of process flow, striving for excellence.